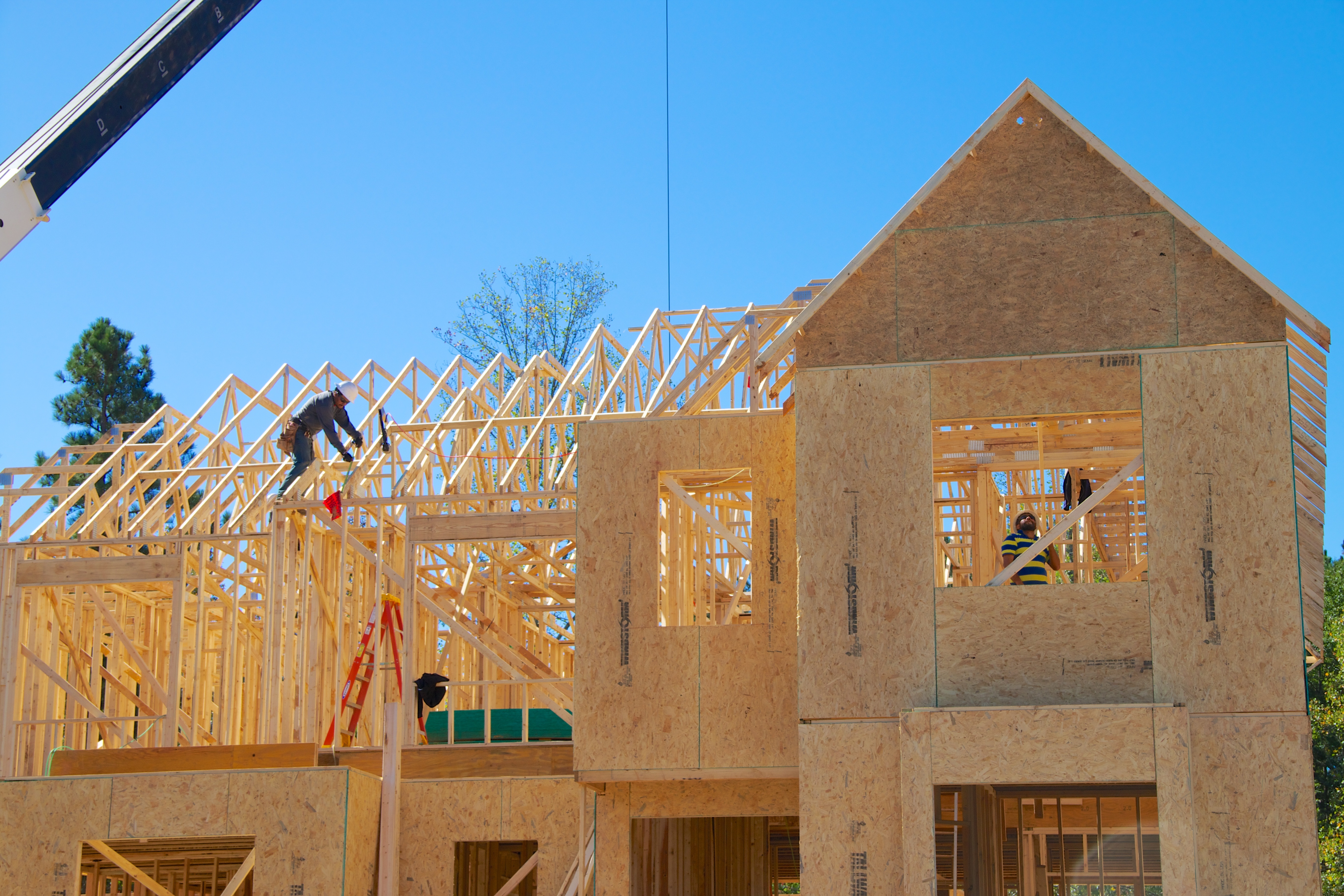
In an age of growing concern for energy efficiency, sustainability and climate change considerations, timber is enjoying a resurgence in popularity for construction projects. Modern timber frame homes can be classic and refined, or ultra-contemporary with jaw-dropping “curb appeal.” Wood is an effective insulator. It uses less carbon during the construction process than steel or concrete. In fact, it’s a natural material that absorbs carbon from the atmosphere and stores it indefinitely.
A timber frame is extremely durable, with impressive longevity. Timber in architecture has a long, proud history. Sources place the first timber frame buildings in 200 BC India. Many European medieval timber frame structures and 17th to 18th century American timber homes are still in use. Do you want to build your own timber home? Keep reading to learn more!
What is Timber Used for in Construction?
In modern construction, timber is used for many purposes, from structural pieces like columns, beams and planks, to roofing, foundation form work and braces. Timber is frequently used, along with concrete and steel, to build bridges. Other examples of industrial timber construction are railway sleepers (support for the rails), piers and jetties. As people become more aware of the advantages of timber frame construction, it is likely that timber home/office buildings and other structures will one day replace steel and concrete.
What is Heavy Timber?
Heavy timber are pieces of lumber that are at least 5 inches by 5 inches. In timber framing, these heavy timbers are mostly used for posts and beams — that is, the weight-bearing parts of the home. These large lumber dimensions can be used for long spans that will support heavy loads. They’re also highly fire resistant. Heavy timber should not be confused with the standard 2” x 4” lumber that’s used for stick framing. In stick framing, these pieces of wood are attached with nails. In timber framing, nails are not used. Instead, heavy timbers are joined by mortise and tendon joints (with hardwood pegs), lap joints or scarf joints.
What Type of Construction is Heavy Timber Used For?
Traditionally, heavy timbers used in timber frame construction were hand sawed or hewn with axes. The parts of a heavy timber frame are known as beams, posts, jetties, braces and trusses. Unlike stick-built frames, which require load-bearing walls, timber frame homes use long, strong timbers in a vertical and horizontal framework, and the frame bears the weight of the entire structure. What this means is that interior walls are not needed, and it’s possible to have cathedral ceilings.
In heavy timber construction, instead of using nails or screws, timbers are joined either with mortise and tenon joinery and wooden pegs, or more modern wood or metal connectors. There are different types of joinery, such as dovetail, tongue, brace, fork mortise and tendon and shouldered.
Timber framing lends itself especially well to the open floor plans that are popular in today’s real estate market. The timber frame is extremely versatile, allowing for any type of exterior cladding and interior design. Cladding can be anything from classic timber weatherboard to metal, stone tiles or brick clips. Inside, there can be exposed beams created from recycled timber, fireplaces, railings and staircases, and a wide range of decorative features.
Today’s Heavy Timber Construction
Modern timber framing bears little resemblance to techniques from ancient times. CAD/CAM software is used to generate the design and drive CNC technology, which uses computer numerical control to convert an entire timber frame into numbers. The machine then automatically cuts each timber precisely to exact specifications. Everything is pre-made, test fit and then broken down for shipping. Installers at the location put it together and raise it on top of the foundation.
Modern engineering eliminates tiring hand labor, increases production, lowers labor costs and makes timber frame homes more affordable. It also drastically reduces the lead times.
Modern Timber Frame Homes and Energy Efficiency
Timber frame houses are very popular now because of their energy efficiency. Wood is a better insulator than steel or masonry. It’s lightweight, very strong, has a better R value and superior thermal mass. Timber provides greater thermal storage capacity than regular insulation, so it’s slower to heat up or cool down. A timber frame creates a buffer for the interior environment, which reduces temperature swings. This leads to significant energy savings, making modern timber frame homes highly appealing to cost-conscious, environmentally-aware consumers.
Since the timber frame design is so open, there is greater capacity for insulation. One type of insulation system commonly seen in timber frame construction uses Structural Insulated Panels (SIPs). These highly efficient panels effectively seal off the interior living area from the outside environment. Compared to fiberglass insulation, SIPs can cut heating and cooling costs in half.
Another option in modern timber framing is the built-up roof system. This special roof design provides vented air space over the insulation that offers important benefits. It helps to minimize moisture buildup and protects the roof from ice dams, UV damage and extreme weather. A built-up roof system also provides uplift and fire protection. All of this makes timber home/office buildings and other structures a very attractive option.
Timber Framing: Traditional Meets High-Tech
At Hamill Creek Timber Homes, this advanced technology is combined with more than 20 years of hand-cutting expertise and specialized equipment. This means that clients can get the highest quality hand-notched reclaimed timber as well as precision-cut newly harvested timber. It also allows for the engineering of custom designs, including unique curved timbers, for exciting contemporary homes.
Build Your Own Timber Home
If you’d like to make your dream of an extraordinary timber home a reality, we recommend that you partner with a highly experienced timber frame company. They’ll be able to expertly guide you from the design through the production, construction and raising process, answering your questions and helping you to make knowledgeable decisions that are based on your location, environmental factors, preferences and budget.
The basic steps to build your own timber home are as follows:
- Choose your location and acquire the land. Important variables include environmental conditions, panoramic views and sun path.
- Research timber frame companies. Hire the best collaborator that can create your ideal timber home while maximizing the value of your estimated cost.
- Decide if you want to use an outside architectural firm or the timber framer’s own designers.
- After you sign off on the design, the crafting and production of your timber frame will begin. During this time, if you’re working with a general contractor, they can secure the necessary permits and prepare the location site for the timber frame’s arrival.
- During the timber frame construction and raising process, the timber frame is completed, and all joinery is test fit then broken down for shipping. Upon arrival at the site, the team of professional installers will re-construct and raise your timber frame.
- An insulated wall system and roof are installed.
- Additional interior features, floorings, etc. are added.
The best timber frame company will be with you from the very beginning designs through and beyond the raising of the frame at the site. They’ll be able to offer additional materials and consultation throughout the entire project, working directly with you or with you and your contractor. As professionals in the construction business, they will also be able to recommend highly skilled builders, if you don’t already have someone in mind.
Climate Change and The Future of Timber Construction
With the serious climate challenges facing modern society, the future of timber frame construction looks very bright. In addition to offering homeowners long-lasting durability and outstanding energy efficiency, modern timber construction has a keen eye towards the future. Developers are turning back to timber construction to create more environmentally-sound structures. Timber buildings don’t just use less energy to build. The timbers themselves can store atmospheric carbon, and new trees that are planted help to further reduce carbon emissions, for a truly sustainable future.