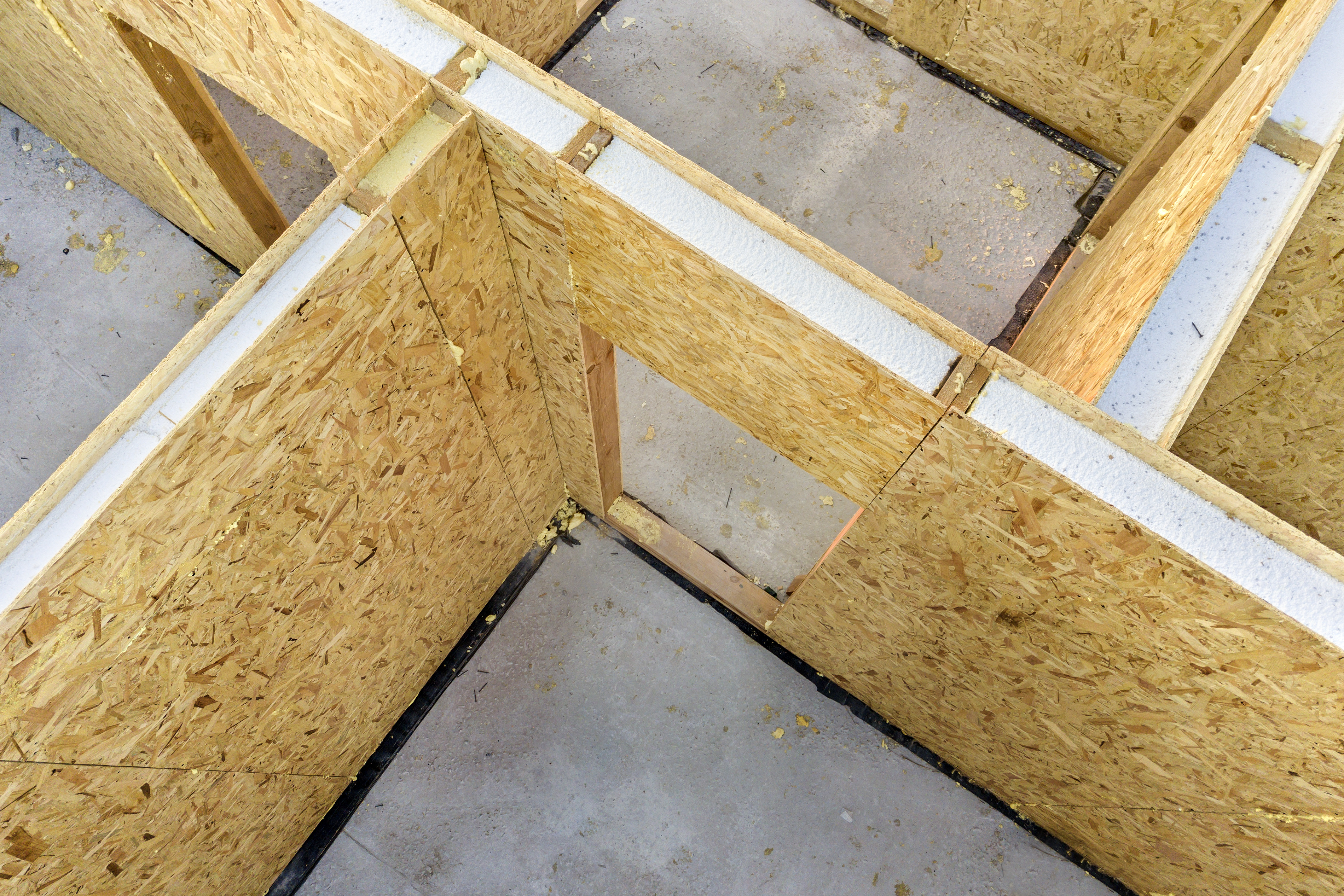
During those chilly winters, it’s nice to know that you always have a warm place to return to after being outside. If you are in the process of building a timber frame home as your cozy refuge from the wind and freezing temperatures, insulating it is a top priority.
Although many types of insulating materials exist, building your home with structural insulated panels (SIPs) kills two birds with one stone. They provide structural support while supporting comfortable temperatures inside.
Here are some facts about structural insulated panels for a timber frame. At Hamill Creek, we want to give you a better idea of what SIPs are and how they can help you enjoy a cozy paradise inside your home during winter.
How do you insulate a timber frame building?
Because of the high ceilings usually associated with timber-framed homes, you cannot simply throw a bunch of insulation into the attic or truss system. That being said there are a few ways to do it in a manner that is both cost-effective and easy. Infill systems come with many challenges i.e. they are hard to air-seal and will blanket the exposed timber inside your home. Seeing the timber frame is the whole point of having one so the majority of timber frame homeowners choose not to go with this option.
To enjoy the beauty inside your home, you must insulate externally. What many find is the best option are structural insulated panels or SIPs. These high-performance panels typically are made of an insulating interior foam between two pieces of oriented strand board. They can be made to fit pretty much any space and are sturdy, easy-to-use, energy-efficient and cost-effective.
Structural insulated panels cost more upfront than some other forms of external insulation. Structural insulated panels disadvantages other than a larger initial investment include pests living in the foam, mold and rot due to moisture build-up and modifying the structural insulated panels on your timber frame can be even more expensive.
Why SIP panels are cost-effective?
Although some exist, the structural insulated panels’ disadvantages aren’t enough to out-weigh their positives for most people. Here are a few ways that make SIPs worthwhile.
- Labor – The hefty initial investment overshadows how much you’ll save on labor. Structural insulated panels can cut framing labor by between 50 and 60 percent as a smaller team is needed to put up the panels.
- Time – Outside of the time it takes to unload the panels, installing SIPs is not time-consuming at all. They are far easier to install than other forms of insulation. A faster construction time means a quicker move-in date.
- Energy – Because they minimize heat leaks in winter, you’ll pay less in energy costs and over time, start to recoup expenses on the high material costs. Structural insulated panels also allow for smaller HVAC units are needed to do the same job, providing more savings.
What are other options to use instead of SIPs?
There are insulated concrete forms (ICFs). These interlocking foam insulation panels are modular, stackable and filled with concrete on-site. They have a high R-value (related to the level of thermal mass) and are tough against floods, winds and even fire. Their inability to stand up to these elemental factors is another one of structural insulated panels’ disadvantages. Even still, structural insulated panels provide a greater thermal mass (R-value) and provide more breathability when the weather is hot.
Are you ready to take the next step in building your dream timber-framed house with cost-effective and durable structural insulated panels but don’t know where to start? Contact the timber frame experts at Hamill Creek to find out more about building your home the right way.