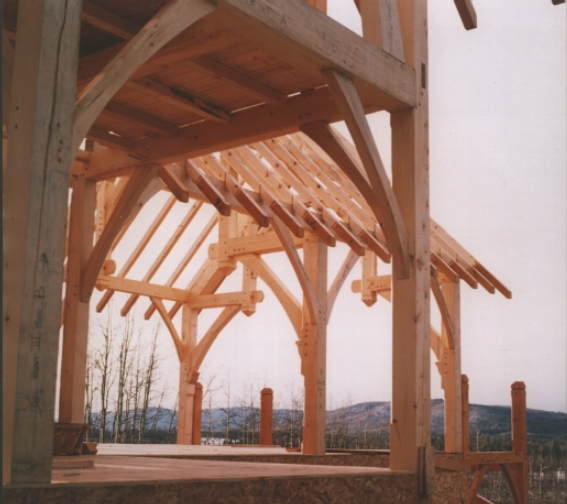
The thoughtfulness and care that goes into building a timber frame house is unsurpassed in the realm of home construction. In creating a beautiful home that’s energy-efficient and long-lasting, every aspect is critical, from the variety of wood used to timber framing tools and methods. There are many options, from the timber species you choose to the type of roof and insulation, and a lot will depend on the home’s location.
In this article, we explore the timber frame construction process, from location considerations and sourcing your timber, to understanding the myriad of timber framing tools that are used in modern-day timber construction. For those considering a custom timber frame home for their family, we’ll also walk you through the basic steps, from log selection to completion.
The Importance of Location in Timber Frame Construction
For maximum energy efficiency, minimal maintenance and region-specific design, the location of your timber home is of utmost importance. If you’re building your house in a cold climate, a south-facing orientation will let you use winter sunlight to help keep the inside warm and reduce energy costs. Part of “best construction practices,” in this case, will be to ensure that foundation footings are below the maximum frost depth. For both cold and hot regions, structural insulated panels (SIPs) create an energy efficient insulation system that provides a strong seal from the outdoor environment, which will reduce both heating and cooling costs for the timber frame building.
How is the Wood Sourced?
There are a few options when sourcing wood for building a timber frame house. Locally sourced timbers are a smart choice for sustainability, as a suitable wood variety for your region and to reduce transportation cost. In green timber construction, homeowners can also choose reclaimed or recycled wood. Reclaimed timber beams come from trees that have been salvaged from forest fires. Recycled timber is antique wood that has been retrieved from old buildings.
What Tools are Needed for Timber Framing?
Through the centuries, timber framing tools have matured, but many of the basic tools and techniques for traditional timber frame building remain the same. It starts with a sawmill that strips the bark from freshly cut logs and cuts them into square timbers. There may be a portable sawmill to work with reclaimed wood. Various types of saws, squares, planers, slot cutters, mortise cutters, drills, chisels, mallets, sanders and possibly an axe may be used. Modern timber framing tools include CNC technology, which converts the timber frame design into precise numbers, which are then used to automatically cut the timbers, greatly reducing construction time. This advanced technology is used alongside traditional timber framing tools to achieve a beautiful and perfectly executed result.
What are the Steps from Log Selection to Installation?
Though the timber framing tools will likely be quite similar, the timber frame construction process will depend upon your builder. However, these are the basic steps for constructing a timber frame building.
- Land acquisition –Choose a site and understand its dynamics in terms of location, the sun path and viewpoints. It is advised that you share your plans with the builder and local officials, so that when it comes time to get permits, it is a smooth process.
- Timber sourcing – Select either freshly cut timber, reclaimed timber or recycled timber, depending upon your needs and preferences.
- Timber frame design selection – Decide if you want to work from a set floor plan or if you have a specific design in mind. Your budget and whether you already have a designer will figure into this decision. At Hamill Creek, you can have professionals work with you to design your dream home, or you can use your own architectural firm and submit the drawings for a quote.
- Timber frame production –Upon approval of the design, your timber frame will be crafted, which takes approximately 4-6 weeks. During this time, the contractor who will be overseeing the construction will obtain the necessary permits.
- Construction and raising of timber frame – The timber frame, after being test fit, is broken down and transferred to the building site. Installers then construct and raise the timber frame, usually in 5-10 days.
- Roof and insulated wall system construction – The roof enclosure and insulated walls are built, which may take about two weeks.
The Bottom Line
Building a timber frame house is a multifaceted operation, but modern timber framing tools and practices can greatly streamline the process so that it takes less time than other building methods. Timber homes are also highly customizable to fit nearly every desire and budget. For more information about designing your ideal timber home, speak to the professionals at Hamill Creek Timber Homes, and benefit from our three decades of timber framing expertise.